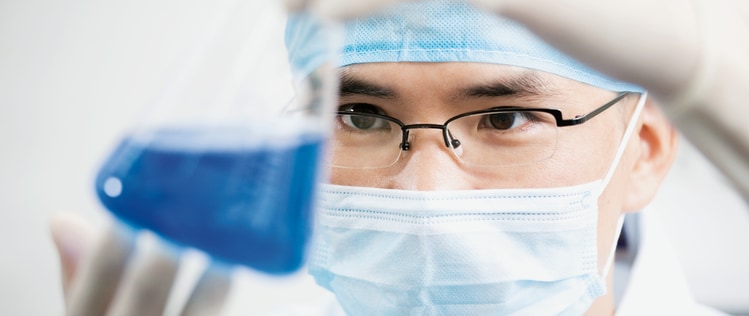
Engineering expertise in gas-enabled applications
Linde engineers are among the most knowledgeable in the world when it comes to gas-enabled applications, which help to improve efficiency, optimisation, and quality across a range of industries. Explore more about the versatility of acetylene in chemical synthesis, benefits of hydrogenation of oil and fat for shelf-life and stability, the use of nitrogen for stirring and mixing liquids, and the use of industrial gases in gas and liquid reactions.
Related areas
Acetylene is a versatile tool in today’s specialty and fine chemical industry for its very special and controllable reactivity in a great variety of synthetic applications. The synthetic potential of acetylene paves the way to various Processes in the chemical industry, e. g. for production of perfume components, vitamins, polymer additives, solvents and surface active compounds.
Edible oils can become rancid when exposed to oxygen. The challenge lies in stabilising these oils to increase their shelf life. One way of achieving this is through hydrogenation. This involves chemically converting fatty acids to reduce the number of double bonds. In practical terms, hydrogenated oil is far more shelf-stable and will not go rancid as quickly as untreated oil. It also has a higher melting point, making it ideal for frying and pastry-making. We supply engineered hydrogen solutions to all areas of the edible oil industry. We can design and operate an on-site production plant or simply deliver liquid hydrogen to meet your specific needs.
Nitrogen gas provides a flexible tool for mixing and storing liquids. It offers considerable advantages over conventional stirring methods. No mechanical devices are needed, so there is no reaction with the liquid and no subsequent cleaning is necessary. The method is readily controllable and offers the added advantage that it introduces no new oxygen into the system while at the same time reducing the oxygen content.
Industrial gases like oxygen, hydrogen, carbon monoxide and carbon dioxide are widely used for synthetic processes in the chemical industry. We have designed a modular, multifunctional stirred reactor test plant (CSTR) for the investigation of a large number of homogeneous gas/liquid reactions. The test plant shown in the picture is perfectly suited for verification of preliminary laboratory results as well as scale-up to medium or large sized technical plants.
Gaseous oxygen is used in many gas/liquid oxidations, for example, in production of hydroperoxides, the oxidative decarboxylations or oxidation of toluene derivatives. Two oxygen processes could be considered for oxidation processes, oxygen enrichment of oxidation air and total substitution of air by oxygen. The benefits of these processes include increased throughput and selectivity and same conversion rate at lower temperatures. We provide a number of service options, these include; feasibility and profitability studies, test runs with our stirred reactor test plant, process calculations to evaluate the effects, supply and installation of gas mixing units and the installation and start-up of oxygen supply systems.
The production of speciality chemicals and active ingredients for the pharmaceutical industry has an increasing demand for synthesis, crystallisation and other unit operations at very low temperatures. With the use of liquid nitrogen (LIN) as a coolant, fluid streams can be chilled to extreme temperatures. Our cryogenic fluid cooling systems are reliable and efficiently chill a process fluid down to –120 °C.
Some of the benefits these units provide include:
•High flexibility with easy to modify temperature profiles
• Comprehensive recording of process parameters
• Cost effective nitrogen used for cooling can be reused in the inert gas net and result in keeping operating
costs to a minimum.
We offer a range of services that include consulting services from initial concept through to final technical
specification, demonstrations and test runs on site. We offer a range of standardised products for you to choose
from (CUMULUS PX5, PX20, PX50, PX100 with 5, 20, 50, 100 kW cooling capacity). If the range of standard units do
not fit your needs we can also provide customised units that are tailor made to your requirements.
Oxidations performed in the heterogeneous gas phase of fixed or fluidized bed reactors are widely used for production of bulk chemicals. Molecular oxygen is the predominant oxidative agent used in these reaction steps. Dependent on the applied process either; air (e. g. for production of maleic or phthalic anhydride), oxygen enriched air (e. g. for production of acrylonitrile) or pure oxygen (e. g. for production of vinylacetate) can be used as a gaseous oxidant. Fluidized bed oxidations are often operated by means of oxidation air, because of its high nitrogen content, it provides an effective fluidizing gas stream for solid particles.
The addition of pure oxygen to the oxidation air or the direct oxygen injection into the reactor can reveal
considerable benefits to the customer:
• Higher plant capacity
• Backup of air compression
• Relief of waste gas treatment
• Enhanced flexibility of plant operation.
In addition, the realization of such an oxygen system comes along with remarkable low investment costs.
Many production plants have problems in keeping the pH value stable in the effluent waste water. In most cases the pH value has to be decreased, and mineral acids are commonly used. But the equipment for this is costly and secondary problems will occur, the use of sulphuric acid will also add sulphates into the water, and hydrochloric acid is highly corrosive for pipes and equipment. Thus you end up with new problems and high operating costs. The handling of such acids is hard to keep safe.
Carbon dioxide forms a weak acid offering a much more accurate and safe pH control, overdosing is now impossible and the equipment is much more simple and less expensive. In addition the buffer capacity of the treated water will improve significantly.
- Acetylene for chemical synthesis
- Hydrogenation of oil and fat
- Mixing and storing liquids using nitrogen
- Gas and liquid reactions
- Reactor and process cooling
- Heterogenous oxidations
- pH regulation
Acetylene for chemical synthesis
Acetylene is a versatile tool in today’s specialty and fine chemical industry for its very special and controllable reactivity in a great variety of synthetic applications. The synthetic potential of acetylene paves the way to various Processes in the chemical industry, e. g. for production of perfume components, vitamins, polymer additives, solvents and surface active compounds.
Downloads
Safety datasheets | Product datasheets & brochures |
---|---|